Tempo di attesa
Un tempo di attesa è il ritardo tra l’inizio e il completamento di un processo. Nelle catene di approvvigionamento, ogni volta che vengono acquistati, trasformati o serviti beni, sono coinvolti tempi di attesa generalmente misurati in giorni. Dal punto di vista della pianificazione, i tempi di attesa sono importanti perché implicano che la maggior parte delle decisioni di routine deve essere presa in anticipo per ottenere l’effetto desiderato, come mantenere la qualità del servizio. La necessità di una previsione della domanda di solito emerge anche dall’esistenza dei tempi di attesa, poiché l’adeguatezza di una decisione - come un riapprovvigionamento delle scorte - dipende da eventi futuri sconosciuti che influenzeranno la catena di approvvigionamento per la durata del tempo di attesa.
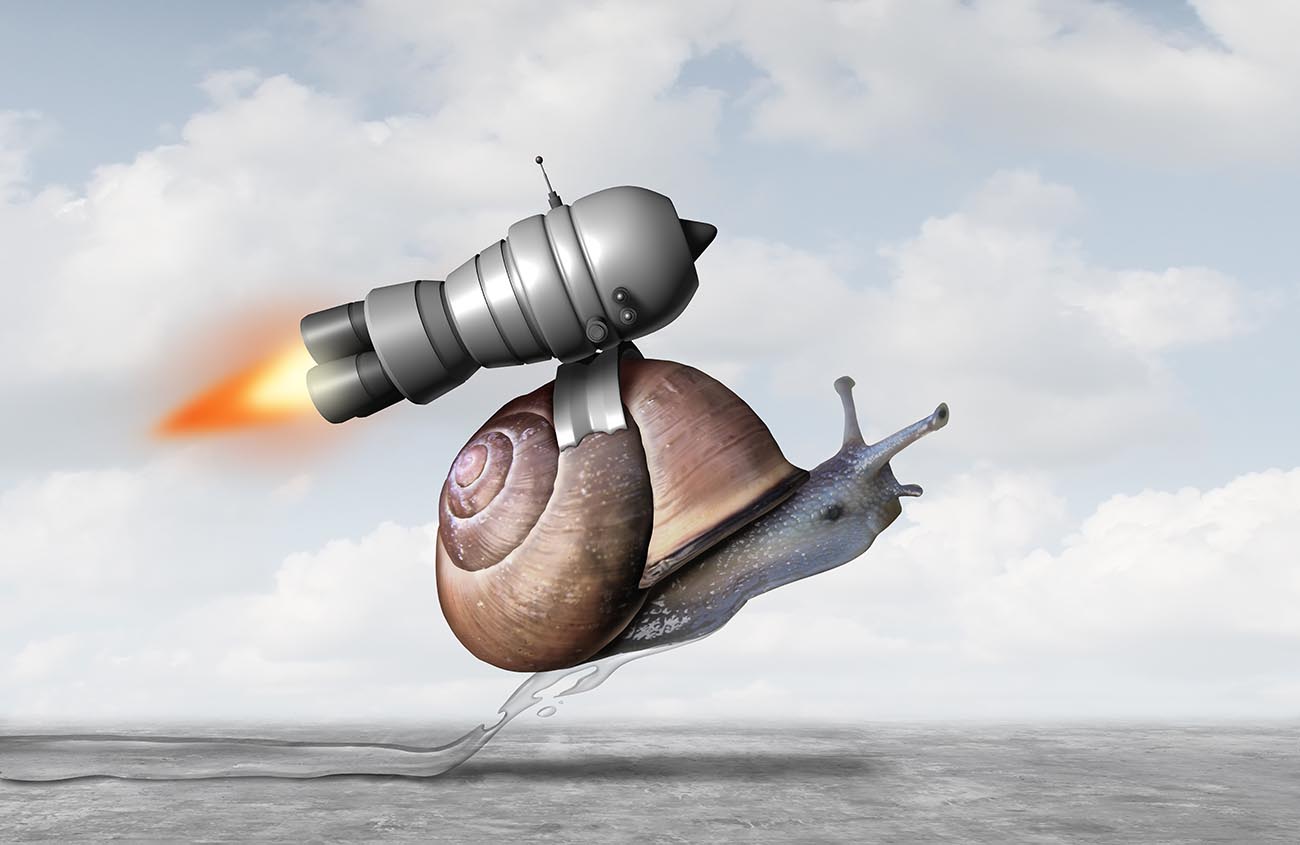
Cause e conseguenze dei tempi di attesa
I tempi di attesa plasmano in gran parte il modo in cui opera la catena di approvvigionamento e la maggior parte dei suoi elementi finanziari, come il capitale di lavoro necessario e il rendimento del capitale impiegato (ROCE). Infatti, tempi di attesa più lunghi implicano che ci vuole più tempo per completare un ciclo di inventario in cui i materiali o i prodotti vengono acquistati, eventualmente trasformati e rivenduti.
I tempi di attesa più lunghi comportano meccanicamente maggiori impegni di magazzino, anche quando le scorte disponibili sembrano rimanere basse. Ad esempio, se un’azienda in Europa ordina merci dall’Asia da consegnare tramite container, dalla data in cui viene effettuato l’ordine di acquisto l’azienda è impegnata a vendere o consumare le merci. Tuttavia, in questa situazione, di solito ci vorranno più di 6 settimane perché i livelli di scorte in Europa riflettano questo impegno.
Inoltre, i tempi di attesa più lunghi aumentano la dipendenza dalla previsione. Nel caso dell’esempio sopra, l’azienda non può limitarsi a passare un ordine di acquisto in base alle sue esigenze attuali; quando l’ordine viene consegnato, la situazione sarà cambiata. I livelli di scorte attuali saranno stati ulteriormente abbassati a causa del consumo in corso e la domanda molto probabilmente sarà cambiata, anche solo a causa della stagionalità.
I tempi di attesa rappresentano un limite inferiore dell’agilità massima che un’azienda può raggiungere. Come regola generale, se le condizioni di mercato cambiano improvvisamente, l’azienda rimane vincolata alle sue decisioni passate per circa la durata dei tempi di attesa. Ci sono vari modi per mitigare questi effetti, a partire dalle condizioni contrattuali con i fornitori. Tuttavia, i rischi sottostanti raramente possono essere eliminati e vengono semplicemente spostati all’interno della catena di approvvigionamento.
Considerando tutti gli impatti negativi dei tempi di attesa più lunghi, ci si potrebbe chiedere perché le aziende optano frequentemente per tempi di attesa che sembrano (soggettivamente) lunghi. Si scopre che ci sono molteplici fattori economici che fanno pendere la bilancia a favore di tempi di attesa più lunghi.
La specializzazione sta guidando tempi di attesa più lunghi: alcuni paesi hanno industrie abbastanza uniche1 che sono difficili o costose da replicare localmente. Tali industrie concentrate sono storicamente emerse principalmente a causa di materiali ad alto valore, che erano facili da trasportare. Tuttavia, anche se gli aerei possono raggiungere qualsiasi punto del globo in meno di 24 ore, le dogane e i processi tendono ad aumentare sostanzialmente i tempi di attesa effettivi quando si considerano i fornitori d’oltremare.
Gli economie di scala si stanno anche orientando verso tempi di attesa più lunghi. Aumentando le dimensioni dei lotti (spesso materializzati come MOQ), i produttori o i trasportatori possono ridurre i loro costi. Tuttavia, man mano che le quantità dei lotti diventano più grandi, il numero dei lotti diventa anche più basso e quindi meno frequente - con tutte le altre cose uguali, in particolare la domanda. Tuttavia, le industrie non sono tutte ugualmente suscettibili alle economie di scala, che tendono a raggiungere un plateau a seconda della tecnologia applicabile.
Ridurre i quantili più alti
Sebbene un tempo di attesa possa essere migliorato riducendo la sua durata media, di solito sono le migliorie relative ai casi peggiori - cioè le situazioni più lunghe - che contano di più. Nelle catene di approvvigionamento, i problemi più grandi - quando misurati in termini di impatto economico - tendono a concentrarsi nella coda: sono i tempi di attesa inaspettatamente alti che causano stock-out o interruzioni nella produzione, non le piccole difficoltà.
Uno dei modi più semplici per valutare questi scenari peggiori consiste nell’utilizzare misurazioni quantili. Ad esempio, se si dice che un fornitore ha un tempo di attesa di 7 giorni per il quantile del 95%, significa che il 95% degli ordini passati a questo fornitore viene consegnato in meno di 7 giorni. Questi quantili “alti”, cioè vicini al 100%, possono discostarsi notevolmente dal tempo di attesa medio. Lo stesso fornitore potrebbe consegnare in media in 2 giorni, che è meno di un terzo della sua stima di quantile alto per lo stesso tempo di attesa.
Al fine di evitare questi problemi di qualità del servizio, tutti i buffer di inventario all’interno della catena di approvvigionamento - indipendentemente dalla metodologia utilizzata - tendono a crescere linearmente, non con la media del tempo di attesa, ma con qualche quantile alto del tempo di attesa. Infatti, i buffer di inventario esistono appositamente per ospitare le variazioni delle condizioni della catena di approvvigionamento. I due fattori dominanti dietro le variazioni inaspettate che influenzano la catena di approvvigionamento tendono ad essere: la domanda variabile e il tempo di attesa variabile.
Diversità dei tempi di attesa
Il tempo di attesa totale dagli ordini di acquisto originali dai fornitori alle consegne ai clienti può di solito essere decomposto in molti, possibilmente dozzine, di passaggi intermedi. Al fine di ridurre il valore del tempo di attesa totale o la sua variabilità, di solito è efficace decomporre questo tempo di attesa totale nei suoi componenti secondari notevoli, che sono più semplici da analizzare e migliorare.
Ad esempio, un grossista che distribuisce merci da fornitori d’oltremare può affrontare:
- Un tempo di attesa per l’ordine, causato dal processo di acquisto settimanale del grossista stesso.
- Un tempo di attesa per l’opportunità, causato dai MOQ imposti dai fornitori.
- Un tempo di attesa per la produzione, richiesto dai fornitori per soddisfare l’ordine di acquisto.
- Un tempo di attesa per il trasporto, richiesto dalla compagnia di trasporto.
- Un tempo di attesa amministrativo, per passare attraverso le dogane.
- Un tempo di attesa per la ricezione, per l’inventario e il controllo di qualità da parte del grossista.
- Un tempo di attesa per la spedizione, richiesto dal centro di distribuzione per soddisfare gli ordini dei clienti.
- Un tempo di attesa per la consegna dell’ultimo miglio, richiesto da un trasportatore per effettuare la consegna al cliente.
Per ogni operazione, di solito è interessante ridurre sia il ritardo medio che la varianza del ritardo.
Tenere traccia di tutte queste operazioni comporta molto lavoro amministrativo, che può essere notevolmente alleviato tramite moderni sistemi informatici, sia attraverso codici a barre e/o RFID. I record elettronici sono tipicamente archiviati nei sistemi informatici delle aziende coinvolte. I benefici si estendono ben oltre l’ottimizzazione dei tempi di attesa, poiché questi sistemi garantiscono la tracciabilità delle merci e, in certa misura, prevengono la riduzione dell’inventario.
Fino alla fine degli anni ‘90, archiviare e elaborare tutti questi record richiedeva costose risorse informatiche, quindi non era sempre economicamente fattibile acquisire e ancor meno conservare tutti i minuti record generati dal flusso di merci fisiche all’interno di una supply chain. Tuttavia, fin dai primi anni 2010, i costi di archiviazione dei dati e di elaborazione sono scesi ben al di sotto del punto in cui le risorse informatiche grezze contano a malapena quando sono coinvolti flussi fisici. Tuttavia, i costi informatici, in particolare le integrazioni di sistema, possono impedire l’acquisizione di questi record elettronici.
Al fine di migliorare i tempi di attesa e quindi ridurre tipicamente i loro alti quantili come discusso in precedenza, sono necessime misurazioni. Le misurazioni dei tempi di attesa dettagliate sono molto utili quando si tratta di analisi delle cause di base. Infatti, poiché le operazioni variano notevolmente da un passo all’altro, la natura dei miglioramenti apportati tende a variare notevolmente.
Tempo di attesa per l’ordine
Il tempo di attesa per l’ordine si riferisce tipicamente al tempo trascorso tra l’ordine del cliente e la consegna delle merci. Questa durata è notevole perché è il “sapore” del tempo di attesa a cui il pubblico in generale - a differenza degli esperti di supply chain - è più abituato. In molti settori al di là del commercio elettronico B2C, il tempo di attesa per l’ordine è strettamente legato alla qualità del servizio. In particolare, le mancanze di magazzino tendono ad essere il fattore dominante che determina tempi di attesa per l’ordine anormalmente lunghi.
Parte della sfida nel migliorare i tempi di attesa per l’ordine non consiste nel ridurre i tempi di attesa stessi, ma nel stabilire le giuste aspettative da parte dei clienti riguardo alla data di consegna. In particolare, diverse grandi aziende di e-commerce sembrano aver adottato da oltre un decennio l’approccio di condividere una stima di previsione del tempo di attesa per l’ordine, che funge da limite superiore probabile del ritardo. Il bias nella stima del ritardo viene introdotto appositamente al fine di ridurre al minimo la frequenza delle situazioni in cui le merci non vengono consegnate in tempo.
Previsione dei tempi di attesa
L’adeguata anticipazione dei tempi di attesa futuri è un ingrediente essenziale per l’ottimizzazione di una supply chain. Come la domanda, anche i tempi di attesa possono e devono essere previsti, sfruttando tipicamente i dati storici esistenti quando rilevanti.
Sebbene la previsione dei tempi di attesa non sia ancora una pratica diffusa tra i team di pianificazione della “domanda”, va notato che la maggior parte delle ciclicità che si applicano alla domanda si applicano anche ai tempi di attesa. Ad esempio, i tempi di attesa tendono a mostrare stagionalità, effetti del giorno del mese e del giorno della settimana. I tempi di attesa cambiano nel tempo. Ad esempio, un fornitore può rivedere i propri processi per ridurre i tempi di attesa o aumentarli per abbassare i costi. Anche la quasi-stagionalità è importante, con eventi come il Capodanno cinese, che periodicamente gonfia i tempi di attesa poiché molte fabbriche in Asia sono chiuse durante questo periodo.
Le previsioni probabilistiche dovrebbero essere preferite per i tempi di attesa, perché come indicato in precedenza, sono i quantili alti che guidano le implicazioni economiche dei tempi di attesa. I costi e i problemi si concentrano nella coda della distribuzione. Tuttavia, sottolineiamo subito che le distribuzioni normali (Gaussiane) non dovrebbero essere utilizzate per i tempi di attesa. Come regola generale, i tempi di attesa non sono mai distribuiti normalmente e l’utilizzo di un tale modello porta a una vasta sottovalutazione dei quantili alti, che a sua volta è la ricetta per generare un flusso continuo di problemi di servizio.
I tempi di attesa possono essere modellati in modo più appropriato come distribuzioni multimodali che riflettono il sistema fisico sottostante. Ad esempio, quando si avvia una linea di produzione, i tempi di attesa della produzione tendono ad essere altamente prevedibili, tranne se manca uno dei materiali grezzi, nel qual caso il tempo di attesa della produzione potrebbe richiedere considerevolmente più tempo. Pertanto, la modellizzazione pratica della distribuzione di probabilità coinvolge tipicamente una combinazione di distribuzioni discrete e parametriche.
La previsione probabilistica del tempo di attesa dovrebbe produrre una variabile casuale discreta per ogni fase interna. Spesso è ragionevole assumere che queste fasi interne siano statisticamente indipendenti (ad esempio, il ritardo imposto dalla dogana è strettamente indipendente dal ritardo di produzione). In questi casi, le variabili casuali possono essere sommate in modo canonico, il che comporta tecnicamente un’operazione di convoluzione eseguita sulle distribuzioni sottostanti.
Modalità controllate
Sebbene il modello di previsione dei tempi di attesa probabilistico appropriato sia tipicamente multimodale, ci sono certe modalità che richiedono un trattamento specifico se è coinvolto un grado di controllo, a differenza di osservazioni passive. Ad esempio, se è possibile richiedere una spedizione aerea o una spedizione via mare da un fornitore, le due modalità di trasporto non dovrebbero essere raggruppate insieme dal punto di vista delle previsioni. È coinvolto un grado di controllo. Ogni modalità di trasporto ha la propria variabilità e quindi sono necessarie due previsioni distinte.
Accoppiamento della domanda
Poiché le capacità di produzione sono limitate quando la domanda aumenta rapidamente, anche il tempo di attesa della produzione tende ad aumentare. Questo accoppiamento tra domanda e tempo di attesa influisce negativamente sulla qualità del servizio, poiché diminuisce la capacità dell’azienda di mitigare un aumento della domanda attraverso ordini di acquisto o di produzione extra, proprio a causa del tempo di attesa extra coinvolto. Pertanto, può essere rilevante avere un modello predittivo congiunto sia per la domanda che per il tempo di attesa, poiché i buffer di inventario richiesti dipendono da due fattori.
Tuttavia, considerando le unità di produzione che hanno abbastanza flessibilità per (ri)organizzare le loro code di lavoro, i tempi di attesa osservati dipendono pesantemente dalla prioritizzazione data a ciascun lavoro specifico. Pertanto, la modellizzazione appropriata del tempo di attesa predittivo dovrebbe tenere conto dell’aspetto della coda del problema, poiché i tempi di attesa possono variare drasticamente a seconda delle scelte di prioritizzazione arbitrarie. Questo grado extra di controllo può essere sfruttato per mitigare l’impatto di un aumento della domanda.
Domanda di attesa
La domanda di attesa rappresenta la quantità di articoli da servire durante la durata del tempo di attesa. Questo valore è particolarmente interessante perché per evitare le scorte esaurite, il totale delle scorte (somma delle scorte disponibili più le scorte in ordine) deve rimanere al di sopra della domanda di attesa in ogni momento. Quando il totale delle scorte scende al di sotto del tempo di attesa, è garantito che si verifichi una scorta esaurita.
Supponendo che sia possibile produrre previsioni probabilistiche sia per la domanda futura che per il tempo di attesa futuro, diventa possibile calcolare stime dei quantili (alti) della domanda di attesa, come definito da:
Dove:
- $${0≤τ≤1}$$ è l’obiettivo della stima del quantile
- $${y}$$ è la domanda, che varia nel tempo
- $${L}$$ è il tempo di attesa
- $${Qτ[..]}$$ è il quantile della funzione interna a valori reali
- $${Ω}$$ è l’insieme dei possibili risultati
- $${t}$$ è il tempo, 1 è il primo periodo futuro
- $${y_ω}$$ è la domanda associata al risultato $${ω}$$
- $${L_ω}$$ è il tempo di attesa associato al risultato $${ω}$$
Questa stima del quantile della domanda di attesa è interessante quando si cerca di mantenere un livello di servizio target. Supponendo un semplice modello di inventario con un singolo SKU, un singolo fornitore e senza MOQ, la quantità da riordinare in ogni momento può essere definita dalla formula:
Dove:
- $${InMagazzino}$$ è la scorta disponibile
- $${InOrdine}$$ è la scorta in ordine
Questa formula assume implicitamente che nessuna domanda venga persa in caso di scorte esaurite. Questa assunzione non è ragionevole in molte situazioni, ad esempio nel settore del commercio al dettaglio, dove tipicamente i clienti rinunciano, optano per un sostituto o scelgono un concorrente anziché semplicemente posticipare il consumo. Per eliminare questa assunzione, l’impatto della domanda persa deve essere esplicitamente modellato. Questo è particolarmente importante quando la domanda è altamente stagionale, poiché le merci che diventano disponibili dopo il picco stagionale possono rimanere invendute o inutilizzate per un lungo periodo di tempo.
Cicli di feedback guidati dal tempo di attesa
Il tempo di attesa può essere visto come un fattore di input per calcolare il riordino, come dettagliato nella sezione precedente. Tuttavia, il tempo di attesa stesso dipende dal programma di ordinazione (o produzione). Inoltre, il programma stesso è tipicamente concepito per essere adatto per raggiungere economie di scala previste raggiungendo la quantità di ordine economica desiderata (EOQ), la quantità minima di ordine (MOQ) o la dimensione nominale del lotto di produzione.
Pertanto, i professionisti della supply chain si trovano spesso di fronte a un ciclo di feedback tra la decisione che deve essere presa oggi (riordino e ordinazione) e il momento in cui ci si aspetta che questa decisione venga ripetuta in futuro. In parole più semplici, la quantità da ordinare oggi dipende dalla data del prossimo riordino: un riordino successivo significa che è necessaria una quantità maggiore. Tuttavia, la data del prossimo riordino è influenzata anche dal riordino del giorno presente: un riordino immediato maggiore significa una data successiva per il prossimo riordino.
Poiché la modellazione esplicita e l’ottimizzazione numerica di questo ciclo di feedback sono complesse, i professionisti della supply chain stabiliscono spesso un programma approssimativo (ad esempio un ordine a settimana o al mese), in linea con le quantità target per raggiungere la dimensione desiderata dell’ordine (cioè l’EOQ, MOQ o la dimensione del lotto). Questo programma viene quindi considerato rigido, consentendo alle quantità di riordino di variare secondo necessità. Tuttavia, l’approccio del programma fisso introduce inefficienze di progettazione, poiché la supply chain non sfrutta tutte le sue possibilità di azione.
È possibile sviluppare soluzioni numeriche migliori per affrontare nativamente questo aspetto del ciclo di feedback. Gli algoritmi coinvolti in tali soluzioni rientrano tipicamente nell’ambito dell’apprendimento per rinforzo. Tuttavia, dettagliare questi algoritmi va oltre lo scopo del presente documento.
Problemi specifici per settore
I tempi di attesa variano e la prospettiva adeguata varia tipicamente a seconda del settore considerato. Nella sezione seguente, esamineremo alcuni settori che presentano sfide specifiche rilevanti per i tempi di attesa.
Durata di conservazione per i prodotti freschi
I prodotti freschi sono altamente deperibili e, di conseguenza, hanno una breve durata di conservazione. Ridurre i tempi di attesa è tipicamente fondamentale per preservare il valore di mercato dei prodotti da esporre il più a lungo possibile. Pertanto, quando si bilanciano le opzioni (imballaggio, trasporto) che influenzano i tempi di attesa, tali opzioni influenzano non solo la qualità del servizio, ma spesso anche il ricavo atteso e lo spreco atteso generato dall’intera supply chain.
Inoltre, i marchi o i distributori si trovano tipicamente di fronte a diverse opzioni di approvvigionamento con scambi tra tempi di attesa e durata di conservazione distinti. Ad esempio, un marchio può acquistare direttamente dal produttore, il che comporta un lungo tempo di attesa ma, una volta ricevuti i prodotti, una lunga durata di conservazione; oppure il marchio può acquistare da un grossista, il che comporta un breve tempo di attesa, ma la ricezione di prodotti con una breve durata di conservazione. In queste situazioni, una corretta ottimizzazione della supply chain bilancia le due opzioni, il che a sua volta richiede un’analisi predittiva dei rispettivi tempi di attesa e delle durate di conservazione.
Tempo di riparazione (TAT) per MRO
Gli MRO (Manutenzione Riparazione e Revisione) gestiscono componenti riparabili. Per ogni cambio di componente, deve essere disponibile un componente riparabile mentre il componente smontato non è riparabile. Il ritardo totale dalla richiesta di cambio del componente alla disponibilità rinnovata dell’unità riparabile è chiamato tempo di riparazione.
La scorta di componenti tenuta dagli MRO dipende direttamente dal TAT. Infatti, se gli MRO avessero la capacità (teorica) di riparare istantaneamente un componente non riparabile, non ci sarebbe bisogno di scorta. Di conseguenza, la previsione e l’ottimizzazione dei tempi di attesa tendono ad essere ancora più critiche rispetto alla previsione della domanda, per quanto riguarda gli MRO.
L’accento sull’analisi del TAT (rispetto all’analisi della domanda) è tipicamente amplificato dalla natura delle riparazioni non programmate, che sono precisamente dovute a guasti che comportano un certo grado di incertezza irriducibile nell’esecuzione dei processi fisici sottostanti - cioè se ci fosse un modo per affrontare il problema in modo proattivo, allora le diagnosi trasformerebbero quelle operazioni in riparazioni programmate.
Logistica inversa per il commercio elettronico
La maggior parte dei commerci elettronici per i consumatori nella maggior parte dei paesi offre oggi la possibilità di restituire la merce se il consumatore non è soddisfatto di ciò che ha ricevuto. Tuttavia, il tasso di resi dei consumatori varia notevolmente da un paese all’altro, principalmente per motivi culturali. Ad esempio, nel commercio elettronico di moda veloce, i consumatori tedeschi mostrano tipicamente tassi di reso superiori al 50%. Questi alti tassi sono determinati in parte dall’abitudine di ordinare più taglie e restituire tutte le taglie tranne una.
Quando i tassi di reso sono elevati, il rivenditore online deve prevedere che una parte consistente della merce tornerà effettivamente; altrimenti, il rivenditore rischia di trovarsi sistematicamente con eccessi di stock quando gli articoli tornano, dopo che sono stati effettuati gli ordini di rifornimento. Tuttavia, ci sono tre incertezze riguardo ai resi futuri: in primo luogo, se gli articoli verranno restituiti o meno, in secondo luogo, se gli articoli supereranno il controllo di qualità dopo essere stati ricevuti e, in terzo luogo, quanto tempo sarà trascorso prima che gli articoli possano essere rivenduti.
Questi problemi di previsione sono abbastanza adatti ad un’analisi strutturata altamente specifica. Infatti, il numero massimo di articoli che possono essere restituiti in qualsiasi momento è limitato dal volume delle spedizioni recenti. Porre un limite agli eventi estremi è di primario interesse dal punto di vista della supply chain. Inoltre, quando ci si trova di fronte alla situazione “3 taglie scelte, 2 taglie restituite”, è possibile prevedere con grande certezza la frazione degli ordini dei consumatori che verranno restituiti.
Aziende di leasing
Le aziende di leasing, come le società di leasing di automobili o di mobili per ufficio, si trovano in situazioni parzialmente simili a quelle degli MRO, ma non del tutto. Infatti, il livello adeguato di inventario dipende dalla domanda futura, ma anche dai tassi futuri di ritenzione, poiché l’inventario ritorna all’azienda di leasing alla fine del contratto di locazione. Poiché l’azienda di leasing non ha il pieno controllo sulla durata del contratto di locazione, queste durate devono essere previste al fine di ottimizzare l’inventario. La durata di questi periodi di ritenzione e il loro effetto sull’inventario possono essere analizzati e previsti attraverso l’analisi dei tempi di attesa regolari.
Tuttavia, la maggior parte delle aziende di leasing ha un certo grado di controllo sulla durata di ritenzione tramite la loro politica dei prezzi e le offerte speciali che possono concedere ai loro clienti. Allo stesso modo di un rivenditore che può aumentare la domanda di un prodotto mettendolo in promozione, un’azienda di leasing può aumentare la durata di ritenzione offrendo condizioni più favorevoli. Pertanto, nelle situazioni di leasing, l’analisi dei prezzi è strettamente intrecciata all’analisi dei tempi di attesa.
Antipattern dei tempi di attesa
Il termine “antipattern” si riferisce a pratiche, processi o strumenti che sono intesi come soluzioni ma non riescono a fornire i risultati attesi. Nelle supply chain, i tempi di attesa sono soggetti a una serie di antipattern che esamineremo in questa sezione.
Mancata valorizzazione
I tempi di attesa sono una delle principali ragioni per cui la pianificazione e la previsione sono importanti dal punto di vista della gestione della supply chain. Tuttavia, i tempi di attesa - come fenomeno da modellare e plasmare - di solito ricevono solo una piccola frazione dell’attenzione rispetto ad altri fenomeni concorrenti, come la domanda. Ci sono molti istituti dedicati alla “previsione della domanda”, ma nessuno dedicato alla “previsione dei tempi di attesa”. Questo squilibrio significativo in termini di allocazione degli sforzi porta spesso a situazioni in cui le analisi quantitative vengono effettuate fino al grammo - sul lato della domanda - per poi arrotondarle alla tonnellata più vicina - sul lato dei tempi di attesa. La maggior parte dei settori richiede che i tempi di attesa siano cittadini di prima classe dell’ottimizzazione della supply chain - al pari della domanda -, sia in termini di processo che di strumenti.
Sovrasfruttamento
Nella maggior parte delle supply chain, la maggior parte delle scorte - compresi i materiali grezzi e i semilavorati - trascorre la maggior parte del tempo immobile in attesa della prossima operazione. Le code di lavorazione tendono a formarsi ad ogni singolo passaggio della supply chain, e ogni coda ha un proprio tempo di attesa. Tuttavia, all’aumentare dell’utilizzo di qualsiasi risorsa, il tempo di attesa nella coda tende ad avvicinarsi all’infinito. Pertanto, il tasso di utilizzo delle risorse è un compromesso tra l’ammortamento della risorsa stessa e i tempi di attesa coinvolti. Questo compromesso consiste nel bilanciare i rendimenti decrescenti dei tassi di utilizzo più elevati con i tempi di attesa che crescono in modo esponenziale.
Volare a occhi chiusi
Migliorare il tempo di attesa di solito inizia assegnando correttamente la responsabilità alla parte specifica del processo che causa il ritardo evitabile più grande. Tuttavia, le misurazioni dei tempi di attesa stessi possono essere fuorvianti. Ad esempio, quando si misura un tempo di attesa del fornitore, se i pallet consegnati spesso rimangono non elaborati in attesa della loro ricezione elettronica su un molo, la misurazione può inflazionare notevolmente il tempo di attesa del fornitore, mentre il processo responsabile è la ricezione stessa. Questi problemi di solito non possono essere affrontati attraverso l’analisi dei dati, ma richiedono osservazioni sul campo per capire se il processo di acquisizione dei dati può essere affidabile o meno. Inoltre, la stessa acquisizione di “top” elettronici, poiché rappresenta un carico di lavoro aggiuntivo per il personale, può aumentare il tempo di attesa complessivo - il che vanifica l’intento originale.
Emergenza LIFO
Elaborare lavori o ordini con un ordine FIFO (first in, first out), è quasi sempre un requisito per garantire una qualità di servizio ragionevole. Infatti, le violazioni del principio FIFO generano in modo erratico tempi di attesa eccessivamente lunghi. Tuttavia, a livello fisico, l’ordine LIFO (last in, first out) tende a emergere naturalmente in molte situazioni, e sono necessari sforzi specifici per evitare queste situazioni LIFO emergenti. Ad esempio:
- Ogni ordine di lavoro in arrivo (picking, produzione, riparazione, ecc.) viene automaticamente stampato come “scheda di lavoro”. Tutte le schede di lavoro in arrivo vengono stampate in una scatola. Tuttavia, a causa della natura del processo di stampa, gli ultimi lavori in arrivo si trovano in cima alla pila, indirizzando gli operatori verso il LIFO.
- Se un nastro trasportatore risulta troppo corto, le merci tendono a traboccare dal nastro trasportatore e possono essere messe a terra all’inizio del nastro trasportatore. Rapidamente, si forma un mucchio di merci, e le merci che sono state presenti per più tempo si trovano alla base della pila. Lo smontaggio delle merci segue l’ordine LIFO.
- Quando scatole o pallet vengono scaricati su un molo attraverso un flusso di trasportatori, a meno che il molo non venga svuotato dopo ogni operazione di scarico, le merci appena arrivate tendono a essere messe davanti o sopra quelle precedenti, il che comporta un ordine LIFO successivamente, quando le merci vengono elaborate.
Note
-
A partire dal 2020, ci sono solo tre paesi che producono RAM (Random Access Memory), un componente hardware fondamentale dei computer moderni. Ci sono anche tre paesi che rappresentano circa il 90% delle riserve e della produzione mondiale di litio, un elemento essenziale delle batterie moderne. ↩︎