Metodo di inventario Min/Max
Il metodo di ordinazione dell’inventario Min/Max è un meccanismo di riordino di base supportato da molti ERP e altri tipi di software di gestione dell’inventario. Il valore “Min” rappresenta un livello di stock che attiva un riordino e il valore “Max” rappresenta un nuovo livello di stock target dopo il riordino. La differenza tra Max e Min viene spesso interpretata come la EOQ (Quantità Economica di Ordine). E sebbene la pianificazione dell’inventario Min/Max sia un metodo abbastanza grezzo per l’ordinazione dell’inventario, le impostazioni Min/Max possono essere regolate dinamicamente per offrire una migliore performance dell’inventario.
Prospettiva storica
Il metodo Min/Max è stato uno dei primi metodi di riapprovvigionamento automatizzati utilizzati nei software aziendali dedicati alla gestione dell’inventario. Il principale vantaggio di questo metodo è la sua estrema semplicità di implementazione.
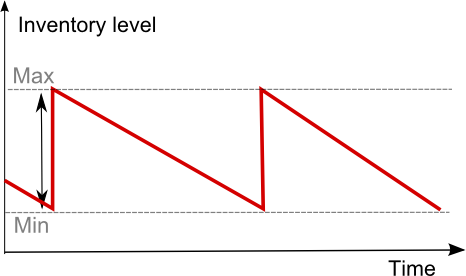
Questo metodo tiene traccia del livello totale di stock attuale, che è tipicamente la somma dello stock disponibile più lo stock in ordine per ogni singolo SKU. Quando lo stock totale raggiunge il valore Min, viene attivato un riordino. La quantità di riordino mira al valore Max per il nuovo livello totale di stock, quindi la quantità di riordino è la differenza tra Max e Min (cioè Max meno Min).
Nella sua forma originale, l’ordinazione Min/Max era considerata un metodo abbastanza statico di controllo dell’inventario in cui i valori Min/Max venivano raramente modificati, forse qualche volta all’anno. L’Analisi ABC veniva spesso utilizzata per guidare gli operatori a dedicare più tempo alla revisione degli articoli “A” che tradizionalmente richiedono più attenzione rispetto agli articoli “B” o “C”.
Regolazione dinamica delle impostazioni Min/Max
Una delle sfide che le aziende devono affrontare per ottimizzare il proprio inventario è che il loro attuale software di gestione dell’inventario non offre necessariamente alcuna logica predittiva avanzata mirata a adattare costantemente e automaticamente i valori Min/Max. Tuttavia, il sistema Min/Max non è di per sé un problema bloccante. Infatti, assumendo che un altro software, dedicato all’ottimizzazione dell’inventario, sia in grado di sovrascrivere i valori Min/Max su base giornaliera per ogni SKU, in questo caso, qualsiasi strategia di controllo dell’inventario rimane possibile.
Per consentire a tale software dedicato di agire e sostituire il metodo Min/Max di base del software principale, possono essere utilizzate le seguenti regole:
- Quando non è necessario effettuare un riordino (secondo il software dedicato all’ottimizzazione dell’inventario), la quantità Min verrà impostata a zero o anche a -1, impedendo l’effettuazione di qualsiasi riordino.
- Quando è necessario effettuare un riordino di quantità X e assumendo che lo stock totale sia S, sia il valore Min che il valore Max dovrebbero essere impostati su X+S.
Seguendo queste regole, il comportamento predefinito di Min/Max che è riordinare al massimo si comporterà esattamente come istruito dal software di ottimizzazione dell’inventario che si trova sopra il software di gestione dell’inventario esistente.
Relazione con i punti di riordino quantili
Il punto di vista della previsione quantile offre un calcolo statistico diretto per i punti di riordino. Dal punto di vista dell’ordinazione Min/Max, quando è necessario effettuare un riordino, sia il valore Min che il valore Max dovrebbero essere aggiornati con il valore del punto di riordino risultante dal calcolo della previsione quantile.
Quindi, mantenere sempre uguali i valori Min e Max porterebbe, in pratica, a un riordino costante ogni volta che viene venduta una singola unità. In realtà, tuttavia, ad eccezione delle situazioni di drop shipping, i riordini non vengono effettuati immediatamente non appena vengono ricevuti gli ordini dei clienti. Invece, i riordini vengono di solito effettuati secondo un programma predefinito.
Quando è presente un programma di riordino, ciò significa semplicemente che i valori Min/Max dovrebbero essere azzerati nei giorni in cui non è previsto alcun riordino per un determinato SKU. In questo caso, le informazioni relative al programma di riordino sono integrate direttamente nelle previsioni quantili attraverso un tempo di consegna scelto.