Délais d'approvisionnement
Les délais d’approvisionnement sont le temps écoulé entre le début et la fin d’un processus. Dans les chaînes d’approvisionnement, chaque fois que des biens sont achetés, transformés ou servis, des délais d’approvisionnement, généralement mesurés en jours, sont impliqués. Du point de vue de la planification, les délais d’approvisionnement sont importants car ils impliquent que la plupart des décisions courantes doivent être prises à l’avance afin de produire l’effet souhaité, tel que le maintien de la qualité de service. Le besoin de prévision de la demande émerge également généralement de l’existence de délais d’approvisionnement, car l’adéquation d’une décision - telle qu’un réapprovisionnement des stocks - dépend d’événements futurs inconnus qui auront un impact sur la chaîne d’approvisionnement pendant la durée du délai d’approvisionnement.
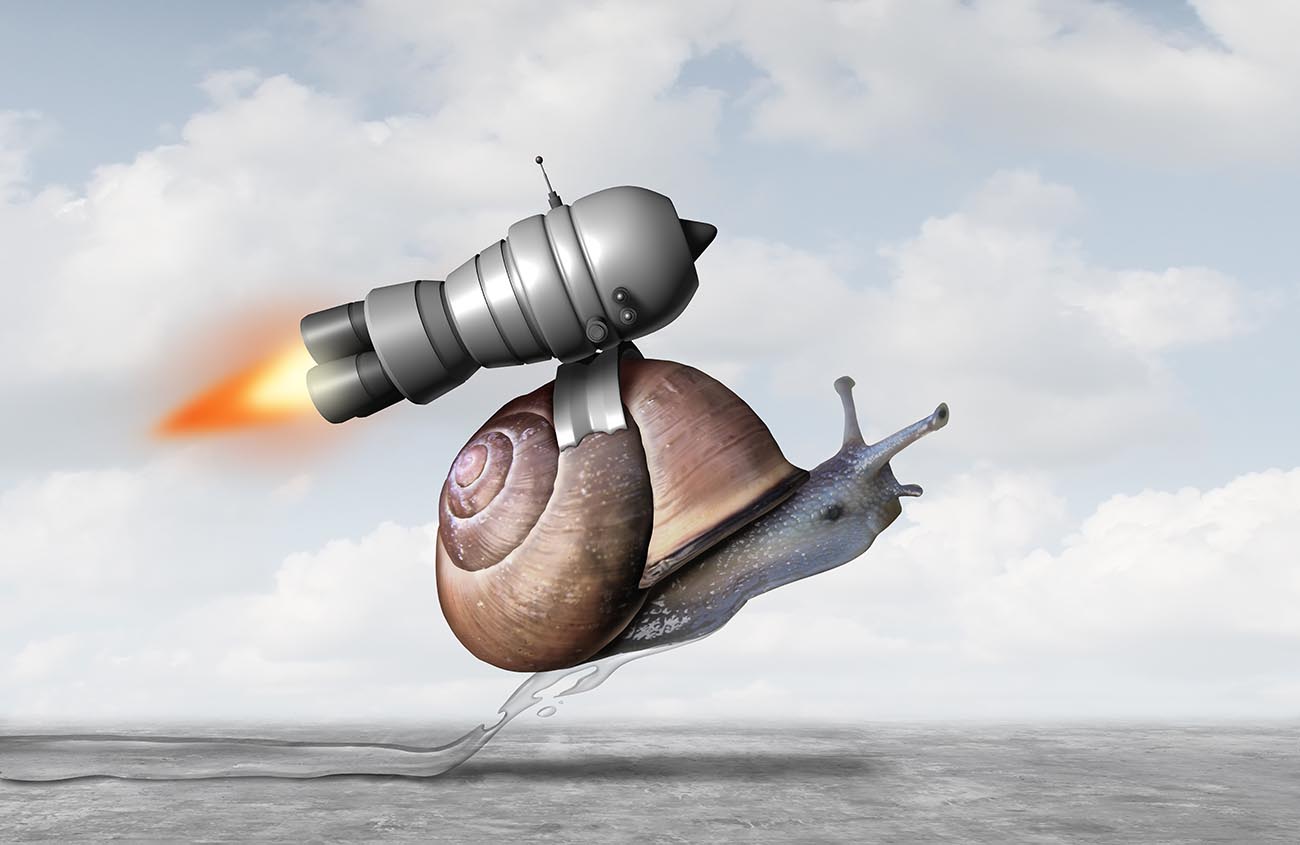
Causes et conséquences des délais d’approvisionnement
Les délais d’approvisionnement façonnent largement le fonctionnement de la chaîne d’approvisionnement et la plupart de ses éléments financiers, tels que le capital de travail requis et le rendement du capital investi (ROCE). En effet, des délais d’approvisionnement plus longs impliquent qu’il faut plus de temps pour terminer un cycle d’inventaire où les matériaux ou les produits sont achetés, éventuellement transformés et revendus.
Des délais d’approvisionnement plus longs entraînent mécaniquement des engagements de stocks plus importants, même lorsque les stocks disponibles semblent rester faibles. Par exemple, si une entreprise en Europe commande des marchandises en Asie pour qu’elles soient livrées par conteneurs, à partir de la date de passation de la commande d’achat, l’entreprise s’engage à vendre ou à consommer les marchandises. Pourtant, dans cette situation, il faudra généralement plus de 6 semaines pour que les niveaux de stock en Europe reflètent cet engagement.
De plus, des délais d’approvisionnement plus longs augmentent la dépendance à l’égard de la prévision. Lorsque l’on reprend l’exemple ci-dessus, l’entreprise ne peut pas se contenter de passer une commande d’achat en fonction de ses besoins actuels ; au moment de la livraison de la commande, la situation aura évolué. Les niveaux de stock actuels auront été réduits davantage en raison de la consommation en cours, et la demande aura très probablement changé, ne serait-ce que en raison de la saisonnalité.
Les délais d’approvisionnement représentent une limite inférieure de l’agilité maximale qu’une entreprise peut atteindre. En règle générale, si les conditions du marché changent brutalement, l’entreprise reste engagée dans ses décisions passées pendant environ la durée des délais d’approvisionnement. Il existe différentes façons d’atténuer ces effets, en commençant par des conditions contractuelles avec les fournisseurs. Cependant, les risques sous-jacents ne peuvent rarement être éliminés et sont simplement déplacés au sein de la chaîne d’approvisionnement.
Compte tenu de tous les impacts négatifs des délais d’approvisionnement plus longs, on peut se demander pourquoi les entreprises optent fréquemment pour ce qui semble être des délais d’approvisionnement (subjectivement) longs. Il s’avère qu’il existe plusieurs facteurs économiques qui penchent en faveur de délais d’approvisionnement plus longs.
La spécialisation entraîne des délais d’approvisionnement plus longs : certains pays ont des industries assez uniques1 qui sont difficiles ou coûteuses à reproduire localement. Ces industries concentrées sont historiquement apparues principalement en raison de matériaux de grande valeur, faciles à transporter. Cependant, même si les avions peuvent atteindre n’importe quel point du globe en moins de 24 heures, les douanes et les processus ont tendance à augmenter considérablement les délais d’approvisionnement réels lorsqu’on considère les fournisseurs étrangers.
Les économies d’échelle penchent également en faveur de délais d’approvisionnement plus longs. En augmentant les quantités de commande (fréquemment matérialisées par les MOQ), les fabricants ou les transporteurs peuvent réduire leurs coûts. Cependant, à mesure que les quantités commandées deviennent plus importantes, le nombre de commandes diminue également et devient donc moins fréquent - toutes choses étant égales par ailleurs, notamment la demande. Néanmoins, toutes les industries ne sont pas également sensibles aux économies d’échelle, qui ont tendance à se stabiliser en fonction de la technologie applicable.
Réduire les quantiles élevés
Bien qu’un délai d’approvisionnement puisse être amélioré en réduisant sa durée moyenne, ce sont généralement les améliorations concernant les pires cas - c’est-à-dire les situations les plus longues - qui importent le plus. Dans les chaînes d’approvisionnement, les plus gros problèmes - mesurés en termes d’impact financier - ont tendance à se concentrer à la fin : ce sont les délais d’approvisionnement inattendus élevés qui provoquent des ruptures de stock ou des interruptions de production, pas les petites perturbations.
L’une des façons les plus simples d’évaluer ces scénarios de pire cas consiste à utiliser des mesures de quantile. Par exemple, si un fournisseur a un délai d’approvisionnement de 7 jours pour le quantile de 95%, cela signifie que 95% des commandes passées à ce fournisseur sont livrées en moins de 7 jours. Ces quantiles “élevés”, c’est-à-dire proches de 100%, peuvent diverger considérablement du délai d’approvisionnement moyen. Le même fournisseur peut livrer en moyenne en 2 jours, ce qui représente moins d’un tiers de son estimation de quantile élevé pour le même délai d’approvisionnement.
Afin d’éviter ces problèmes de qualité de service, tous les tampons d’inventaire au sein de la chaîne d’approvisionnement - quelle que soit la méthodologie utilisée - ont tendance à augmenter linéairement, non pas avec la moyenne du délai d’approvisionnement, mais avec un quantile élevé du délai d’approvisionnement. En effet, les tampons d’inventaire existent précisément pour accommoder les variations des conditions de la chaîne d’approvisionnement. Les deux principaux facteurs qui influencent les variations inattendues ayant un impact sur la chaîne d’approvisionnement sont la demande variable et le délai d’approvisionnement variable.
Diversité des délais d’approvisionnement
Le délai d’approvisionnement total, depuis les commandes d’achat initiales passées aux fournisseurs jusqu’aux livraisons aux clients, peut généralement être décomposé en de nombreuses étapes intermédiaires, pouvant aller jusqu’à des dizaines. Afin de réduire la valeur du délai d’approvisionnement ou sa variabilité, il est généralement efficace de décomposer ce délai d’approvisionnement total en ses sous-composantes notables, qui sont plus simples à analyser et à améliorer.
Par exemple, un grossiste distribuant des marchandises de fournisseurs étrangers peut faire face à :
- Un délai de commande, causé par le processus d’achat hebdomadaire du grossiste lui-même.
- Un délai d’opportunité, causé par les quantités minimales de commande imposées par les fournisseurs.
- Un délai de fabrication, nécessaire aux fournisseurs pour remplir la commande.
- Un délai de transport, nécessaire à la société de transport.
- Un délai administratif, pour passer par les douanes.
- Un délai de réception, pour l’inventaire et le contrôle qualité par le grossiste.
- Un délai d’expédition, nécessaire au centre de distribution pour satisfaire les commandes des clients.
- Un délai de livraison de dernière mile, nécessaire à un transporteur pour effectuer la livraison au client.
Pour chaque opération, il est généralement intéressant de réduire à la fois le délai moyen et la variance du délai.
Le suivi de toutes ces opérations nécessite beaucoup de travail administratif, qui peut être considérablement allégé grâce aux systèmes informatiques modernes, que ce soit par le biais de codes-barres et/ou de RFIDs. Les enregistrements électroniques sont généralement stockés dans les systèmes informatiques des entreprises concernées. Les avantages vont bien au-delà de l’optimisation des délais d’approvisionnement, car ces systèmes garantissent la traçabilité des marchandises et, dans une certaine mesure, empêchent la réduction des stocks.
Jusqu’à la fin des années 1990, le stockage et le traitement de tous ces enregistrements nécessitaient des ressources informatiques coûteuses, ce qui rendait parfois économiquement irréalisable l’acquisition, et encore moins la conservation, de tous les enregistrements minuscules générés par le flux de marchandises physiques au sein d’une chaîne d’approvisionnement. Cependant, depuis le début des années 2010, les coûts de stockage des données et de calcul ont largement diminué, de sorte que les ressources informatiques brutes importent peu chaque fois que des flux physiques sont impliqués. Néanmoins, les coûts informatiques, notamment les intégrations de systèmes, peuvent empêcher l’acquisition de ces enregistrements électroniques.
Afin d’améliorer les délais d’approvisionnement, et donc généralement réduire leurs quantiles élevés comme discuté ci-dessus, des mesures sont nécessaires. Les mesures de délai d’approvisionnement fines sont très utiles lorsqu’il s’agit d’analyser les causes profondes. En effet, comme les opérations varient considérablement d’une étape à l’autre, la nature des améliorations apportées tend également à varier considérablement.
Délai de commande
Le délai de commande fait généralement référence au temps écoulé entre la commande du client et la livraison des marchandises. Cette durée est notable car c’est le “type” de délai d’approvisionnement auquel le grand public - par opposition aux spécialistes de la chaîne d’approvisionnement - est le plus habitué. Dans de nombreuses industries autres que le commerce électronique B2C, le délai de commande est étroitement lié à la qualité de service. En particulier, les ruptures de stock tendent à être le facteur dominant qui entraîne des délais de commande anormalement longs.
Une partie du défi consiste à améliorer les délais de commande non pas en raccourcissant les délais eux-mêmes, mais en fixant les bonnes attentes des clients quant à la date de livraison. En particulier, plusieurs grandes entreprises de commerce électronique semblent avoir adopté depuis plus d’une décennie l’approche consistant à partager une estimation de prévision quantile du délai de commande, qui agit comme une limite supérieure probable du retard. Le biais dans l’estimation du retard est introduit délibérément afin de minimiser la fréquence des situations où les marchandises ne sont pas livrées à temps.
Prévision des délais d’approvisionnement
L’anticipation correcte des délais d’approvisionnement futurs est un ingrédient essentiel pour l’optimisation d’une chaîne d’approvisionnement. Tout comme la demande, les délais d’approvisionnement peuvent et doivent être prévus, en utilisant généralement les données historiques existantes lorsque cela est pertinent.
Bien que la prévision des délais d’approvisionnement ne soit pas (encore) une pratique courante parmi les équipes de planification de la “demande”, il convient de noter que la plupart des cyclicités qui s’appliquent à la demande s’appliquent également aux délais d’approvisionnement. Par exemple, les délais d’approvisionnement ont tendance à présenter une saisonnalité, des effets liés au jour du mois et au jour de la semaine. Les délais d’approvisionnement changent au fil du temps. Par exemple, un fournisseur peut revoir ses propres processus pour réduire les délais d’approvisionnement, ou les augmenter pour réduire ses coûts. La quasi-saisonnalité est également importante, avec des événements tels que le nouvel an chinois, qui gonflent périodiquement les délais d’approvisionnement car de nombreuses usines sont fermées en Asie pendant cette période.
Les prévisions probabilistes devraient être privilégiées pour les délais d’approvisionnement, car, comme indiqué ci-dessus, ce sont les quantiles élevés qui déterminent les implications économiques des délais d’approvisionnement. Les coûts et les problèmes sont concentrés à la queue de la distribution. Cependant, soulignons immédiatement que les distributions normales (gaussiennes) ne doivent pas être utilisées pour les délais d’approvisionnement. En règle générale, les délais d’approvisionnement ne suivent jamais une distribution normale, et l’utilisation d’un tel modèle conduit à une sous-estimation considérable des quantiles élevés, ce qui, à son tour, est la recette pour générer un flux continu de problèmes de service.
Les délais d’approvisionnement peuvent être modélisés de manière plus appropriée sous la forme de distributions multimodales qui reflètent le système physique sous-jacent. Par exemple, lors du déclenchement d’une ligne de production, les délais de production ont tendance à être très prévisibles, sauf si l’une des matières premières vient à manquer, auquel cas le délai de fabrication peut prendre considérablement plus de temps. Ainsi, la modélisation pratique de la distribution de probabilité implique généralement un mélange de distributions discrètes et paramétriques.
La prévision probabiliste du délai d’approvisionnement devrait produire une variable aléatoire discrète pour chaque phase interne. Il est souvent raisonnable de supposer que ces phases internes sont statistiquement indépendantes (par exemple, le retard imposé par les douanes est strictement indépendant du retard de fabrication). Dans ces cas, les variables aléatoires peuvent être sommées de manière canonique, ce qui implique techniquement une opération de convolution effectuée sur les distributions sous-jacentes.
Modalités contrôlées
Alors que le modèle de prévision probabiliste approprié du délai d’approvisionnement est généralement multimodal, certaines modalités nécessitent un traitement spécifique s’il y a un degré de contrôle impliqué, par opposition à des observations passives. Par exemple, s’il est possible de demander un envoi par avion ou par mer à un fournisseur, les deux modes de transport ne doivent pas être regroupés du point de vue de la prévision. Il y a un degré de contrôle impliqué. Chaque mode de transport a sa propre variabilité, et donc, deux prévisions distinctes sont nécessaires.
Couplage de la demande
Comme les capacités de production sont limitées lorsque la demande augmente, le délai de fabrication a tendance à augmenter également. Ce couplage entre la demande et le délai d’approvisionnement a un impact négatif sur la qualité de service, car il diminue la capacité de l’entreprise à atténuer une augmentation de la demande grâce à des commandes d’achat ou de fabrication supplémentaires, précisément en raison du délai d’approvisionnement supplémentaire. Ainsi, il peut être pertinent d’avoir un modèle prédictif conjoint à la fois de la demande et du délai d’approvisionnement, car les stocks tampons nécessaires dépendent de ces deux facteurs.
Cependant, lorsqu’on considère des unités de fabrication qui ont suffisamment de flexibilité pour (re)organiser leurs files d’attente de tâches, les délais d’approvisionnement observés dépendent fortement de la priorisation accordée à chaque tâche spécifique. Ainsi, la modélisation appropriée du délai d’approvisionnement prédictif devrait prendre en compte l’aspect de la file d’attente du problème, car les délais d’approvisionnement peuvent varier considérablement en fonction des choix de priorisation arbitraires. Ce degré supplémentaire de contrôle peut être utilisé pour atténuer l’impact d’une augmentation de la demande.
Demande de délai
La demande de délai représente la quantité d’articles à servir pendant la durée du délai d’approvisionnement. Cette valeur est particulièrement intéressante car, afin d’éviter les ruptures de stock, le stock total (somme du stock disponible et du stock en commande) doit rester supérieur à la demande de délai à tout moment. Lorsque le stock total tombe en dessous du délai d’approvisionnement, une rupture de stock est garantie.
En supposant que des prévisions probabilistes peuvent être produites à la fois pour la demande future et pour le délai d’approvisionnement futur, il devient possible de calculer des estimations de quantiles (élevés) de la demande de délai, comme défini par :
Où :
- $${0≤τ≤1}$$ est la cible de l’estimation de quantile
- $${y}$$ est la demande, variant dans le temps
- $${L}$$ est le délai d’approvisionnement
- $${Qτ[..]}$$ est le quantile de la fonction réelle interne
- $${Ω}$$ est l’ensemble des résultats possibles
- $${t}$$ est le temps, 1 étant la première période future
- $${y_ω}$$ est la demande associée au résultat $${ω}$$
- $${L_ω}$$ est le délai d’approvisionnement associé au résultat $${ω}$$
Cette estimation de quantile de la demande de délai est intéressante lorsqu’il s’agit de maintenir un taux de service cible. En supposant un modèle d’inventaire simple à un seul SKU, un seul fournisseur et sans quantité minimale de commande, la quantité à réapprovisionner à tout moment peut être définie par la formule :
Où :
- $${EnStock}$$ est le stock disponible
- $${EnCommande}$$ est le stock en commande
Cette formule suppose implicitement qu’aucune demande n’est perdue en cas de rupture de stock. Cette hypothèse n’est pas raisonnable dans de nombreuses situations, par exemple dans la vente au détail, où les clients renoncent généralement, optent pour un substitut ou se tournent vers un concurrent au lieu de simplement reporter leur consommation. Afin de lever cette hypothèse, l’impact de la demande perdue doit être explicitement modélisé. Cela est particulièrement important lorsque la demande est très saisonnière, car les biens qui deviennent disponibles après le pic saisonnier peuvent rester invendus ou inutilisés pendant une longue période.
Boucles de rétroaction basées sur le délai d’approvisionnement
Le délai d’approvisionnement peut être considéré comme un facteur d’entrée pour calculer le réapprovisionnement, comme détaillé dans la section précédente. Cependant, le délai d’approvisionnement lui-même dépend de l’ordonnancement (ou de la production). De plus, l’ordonnancement lui-même est généralement conçu pour être adapté afin d’atteindre des économies d’échelle attendues en atteignant la quantité économique de commande (EOQ) souhaitée, la quantité minimale de commande (MOQ) ou la taille nominale du lot de production.
Ainsi, les praticiens de la supply chain sont souvent confrontés à une boucle de rétroaction entre la décision qui doit être prise aujourd’hui (réapprovisionnement et commande) et le moment où cette décision est censée être répétée à l’avenir. En d’autres termes, la quantité à commander aujourd’hui dépend de la date de la prochaine commande : une commande ultérieure signifie qu’une plus grande quantité est nécessaire. Cependant, la date de la prochaine commande est également influencée par la commande immédiate du jour : une commande immédiate plus importante signifie une date ultérieure pour la prochaine commande.
Comme la modélisation explicite et l’optimisation numérique de cette boucle de rétroaction sont complexes, les praticiens de la supply chain établissent souvent un calendrier approximatif (c’est-à-dire une commande par semaine, par mois), en accord avec les quantités cibles pour atteindre la taille de commande souhaitée (c’est-à-dire l’EOQ, MOQ ou la taille du lot). Ce calendrier est ensuite considéré comme rigide, permettant aux quantités de commande de varier selon les besoins. Cependant, l’approche du calendrier fixe introduit des inefficacités par conception, car la supply chain n’exploite pas tous ses degrés de liberté.
De meilleures solutions numériques peuvent être élaborées pour aborder nativement cet aspect de la boucle de rétroaction. Les algorithmes impliqués dans ces solutions relèvent généralement de l’apprentissage par renforcement. Cependant, la description détaillée de ces algorithmes dépasse le cadre du présent document.
Problèmes spécifiques à chaque secteur
Les délais d’approvisionnement varient et la perspective adéquate varie généralement en fonction du secteur considéré. Dans la section suivante, nous passerons en revue quelques secteurs qui présentent des défis spécifiques notables liés aux délais d’approvisionnement.
Durée de conservation des produits frais
Les produits frais sont très périssables, et par conséquent, ils ont une durée de conservation courte. Raccourcir les délais d’approvisionnement est généralement essentiel pour préserver la valeur marchande des produits à exposer autant que possible. Ainsi, lors de l’équilibrage des options (emballage, transport) qui influencent les délais d’approvisionnement, ces options influencent non seulement la qualité de service, mais également les revenus attendus et les déchets attendus générés par l’ensemble de la supply chain.
De plus, les marques ou les distributeurs sont généralement confrontés à plusieurs options d’approvisionnement avec des compromis distincts entre les délais d’approvisionnement et la durée de conservation. Par exemple, une marque peut acheter directement auprès du producteur, ce qui implique un long délai d’approvisionnement mais, à la réception des produits, une longue durée de conservation ; ou la marque peut acheter auprès d’un grossiste, ce qui implique un court délai d’approvisionnement, mais la réception de produits avec une courte durée de conservation. Dans ces situations, une optimisation appropriée de la supply chain équilibre les deux options, ce qui nécessite une analyse prédictive des délais d’approvisionnement et des durées de conservation respectives.
Temps de réparation (TAT) pour les MRO
Les MRO (Maintenance Repair & Overhaul) gèrent les composants réparables. Pour que chaque changement de composant ait lieu, un composant réparable doit être disponible immédiatement tandis que le composant démonté est inutilisable jusqu’à sa réparation. Le délai total entre la demande de changement de composant et la disponibilité renouvelée de l’unité réparable est appelé temps de réparation.
Le stock de composants conservé par les MRO dépend directement du TAT. En effet, si le MRO avait la capacité (théorique) de réparer instantanément un composant inutilisable, il n’y aurait pas besoin de stock. Par conséquent, la prévision et l’optimisation des délais d’approvisionnement sont encore plus critiques que la prévision de la demande, en ce qui concerne les MRO.
L’accent mis sur l’analyse du TAT (par rapport à l’analyse de la demande) est généralement renforcé par la nature des réparations non planifiées, qui sont précisément dues à des pannes impliquant un certain degré d’incertitude irréductible pour effectuer les processus physiques sous-jacents - c’est-à-dire que s’il existait un moyen de résoudre le problème de manière proactive, alors les opérations de diagnostic transformeraient ces réparations en réparations planifiées.
Logistique inverse pour le commerce électronique
La plupart des sites de commerce électronique grand public dans la plupart des pays offrent aujourd’hui la possibilité de retourner les marchandises si le consommateur n’aime pas ce qu’il a reçu. Cependant, le taux de retour des consommateurs varie considérablement d’un pays à l’autre, principalement pour des raisons culturelles. Par exemple, dans le commerce électronique de la mode rapide, les consommateurs allemands présentent généralement des taux de retour supérieurs à 50 %. Ces taux élevés sont en partie dus à l’habitude de commander plusieurs tailles et de retourner toutes les tailles sauf une.
Lorsque les taux de retour sont élevés, le détaillant en ligne doit anticiper qu’une partie importante du stock reviendra effectivement ; sinon, le détaillant court le risque de se retrouver systématiquement avec des surstocks lorsque les articles reviennent après le passage des commandes de réapprovisionnement. Cependant, il existe trois incertitudes concernant les retours futurs : premièrement, si les articles seront retournés ou non, deuxièmement, si les articles passeront le contrôle qualité après réception, et troisièmement, combien de temps s’écoulera avant que les articles puissent être revendus.
Ces problèmes de prévision se prêtent très bien à une analyse structurée hautement spécifique. En effet, le nombre maximal d’articles pouvant être retournés à un moment donné est limité par le volume des expéditions récentes. Mettre une limite aux événements extrêmes est d’un intérêt primordial d’un point de vue de la supply chain. De plus, lorsqu’on est confronté à la situation “3 tailles choisies, 2 tailles retournées”, il est possible d’anticiper avec une grande certitude la fraction des commandes des consommateurs qui seront retournées.
Les entreprises de location
Les entreprises de location, telles que les sociétés de location de voitures ou les sociétés de location de mobilier de bureau, sont confrontées à des situations qui sont partiellement similaires aux situations MRO, mais pas tout à fait. En effet, le niveau approprié des stocks dépend de la demande future, mais aussi des taux de rétention futurs, car les stocks reviennent à l’entreprise de location à la fin de la location. Comme l’entreprise de location n’a pas un contrôle total sur la durée de la location, ces durées doivent être prévues afin d’optimiser les stocks. La durée de ces périodes de rétention et leur effet sur les stocks peuvent être analysées et prévues à travers le prisme des délais d’approvisionnement réguliers.
Cependant, la plupart des entreprises de location ont une certaine maîtrise de la durée de rétention grâce à leur tarification et aux offres spéciales qu’elles peuvent accorder à leurs clients. De la même manière qu’un détaillant peut stimuler la demande d’un produit en le mettant en promotion, une entreprise de location peut prolonger sa durée de rétention en proposant des conditions plus favorables. Ainsi, dans les situations de location, l’analyse des prix est étroitement liée à l’analyse des délais d’approvisionnement.
Les antipatterns des délais d’approvisionnement
Le terme “antipatterns” fait référence à des pratiques, des processus ou des outils qui sont censés être des solutions mais qui ne parviennent pas à fournir les résultats attendus. Dans les chaînes d’approvisionnement, les délais d’approvisionnement sont sujets à une série d’antipatterns que nous examinons dans cette section.
Méconnaissance
Les délais d’approvisionnement sont l’une des principales raisons pour lesquelles la planification et la prévision sont importantes du point de vue de la gestion de la chaîne d’approvisionnement. Pourtant, les délais d’approvisionnement - en tant que phénomène à modéliser et à façonner - ne reçoivent généralement qu’une infime fraction de l’attention accordée à d’autres phénomènes concurrents, tels que la demande. Il existe plusieurs instituts dédiés à la prévision de la demande, mais aucun dédié à la prévision des délais d’approvisionnement. Ce déséquilibre considérable en termes d’allocation des efforts conduit fréquemment à des situations où des analyses quantitatives sont effectuées avec une précision extrême du côté de la demande, pour ensuite les arrondir au tonneau le plus proche du côté des délais d’approvisionnement. La plupart des secteurs d’activité exigent que les délais d’approvisionnement soient des éléments essentiels de l’optimisation de la chaîne d’approvisionnement - au même titre que la demande -, tant en termes de processus que d’outils.
Sur-utilisation
Dans la plupart des chaînes d’approvisionnement, la majeure partie des stocks - y compris les matières premières et les produits semi-finis - passe la majeure partie de son temps immobile et en attente de l’étape suivante. Des files d’attente de traitement se forment à chaque étape de la chaîne d’approvisionnement, et chaque file d’attente est associée à un temps d’attente propre. Cependant, à mesure que l’utilisation de tout actif se rapproche de 100%, le temps d’attente dans la file d’attente se rapproche de l’infini. Ainsi, le taux d’utilisation de l’actif est un compromis entre l’amortissement de l’actif lui-même et les délais d’approvisionnement impliqués. Ce compromis consiste à équilibrer les rendements décroissants des taux d’utilisation plus élevés par rapport à la croissance exponentielle des temps d’attente.
Voler à l’aveugle
Améliorer les délais d’approvisionnement commence généralement par attribuer correctement la responsabilité à la partie spécifique du processus qui cause le plus grand retard évitable. Cependant, les mesures des délais d’approvisionnement eux-mêmes peuvent être trompeuses. Par exemple, lors de la mesure d’un délai d’approvisionnement fournisseur, si les palettes livrées restent fréquemment non traitées en attendant leur réception électronique sur un quai, la mesure peut largement gonfler le délai d’approvisionnement fournisseur, alors que le processus en faute est la réception elle-même. Ces problèmes ne peuvent généralement pas être résolus par l’analyse des données, mais nécessitent des observations sur place pour comprendre si le processus d’acquisition des données peut être fiable ou non. De plus, l’acquisition même des “tops” électroniques, car elle représente une charge de travail supplémentaire pour le personnel, peut elle-même augmenter le délai d’approvisionnement global - ce qui contredit l’intention initiale.
LIFO émergent
Traiter les tâches ou les commandes avec une ordonnance FIFO (premier entré, premier sorti) est presque toujours une exigence pour garantir une qualité de service raisonnable. En effet, les violations du principe FIFO génèrent de manière erratique des délais d’approvisionnement excessivement longs. Cependant, au niveau physique, l’ordonnancement LIFO (dernier entré, premier sorti) tend à émerger naturellement dans de nombreuses situations, et des efforts spécifiques sont nécessaires pour éviter ces situations LIFO émergentes. Par exemple :
- Chaque commande de travail entrante (prélèvement, production, réparation, etc.) est automatiquement imprimée sous la forme d’une “fiche de travail”. Toutes les fiches de travail entrantes sont imprimées dans une boîte. Cependant, en raison de la nature du processus d’impression, les dernières commandes entrantes se trouvent en haut de la pile, orientant les opérateurs vers le LIFO.
- Si un convoyeur est trop court, les marchandises ont tendance à déborder du convoyeur et peuvent être posées au sol au début du convoyeur. Rapidement, un tas de marchandises se forme, et les marchandises qui sont là depuis le plus longtemps se trouvent en bas de la pile. Le dépilement des marchandises suit l’ordonnancement LIFO.
- Lorsque des boîtes ou des palettes sont déchargées sur un quai à l’aide de transporteurs, sauf si le quai est vidé après chaque opération de déchargement, les marchandises fraîchement arrivées ont tendance à être placées devant ou au-dessus des précédentes, ce qui entraîne un ordonnancement LIFO ultérieur, lorsque les marchandises sont traitées.
Notes
-
En 2020, seuls trois pays produisent de la RAM (Random Access Memory), un composant matériel fondamental des ordinateurs modernes. Il existe également trois pays qui représentent près de 90% des réserves et de la production mondiales de lithium, un élément essentiel des batteries modernes. ↩︎